Sealing System Leakage Analysis - Seal Lip
Lack of Wear
Probable Causes | Actions or Countermeasures |
---|---|
No interference with the shaft. | Check seal ID for missing garter spring. Check shaft diameter. Observe shaft for evidence of contact. Look for concave distortion on outside face of seal. |
Very light interference with the shaft. | Check seal ID for low radial load. Look for concave distortion on outside face of seal. |
Seal installed backwards. | Check installation method and teardown report. |
Heavy continuous leakage from startup, possibly from another source. | Check fluid consumption reports-look for excessive media outside the seal area. Check shaft size and seal interference. Leakage may be occurring through a defect; check seal ID and shaft for defects. |
Dynamic lift-off from centrifugal force, flutter or stick slip action. | Check for low radial load and spring presence. Check lip opening pressure on shaft size mandrel. |
Reverse hydrodynamic pumping. | Check shaft rotation direction with helix direction. Check for spiral lead or axial scratches on the shaft. |
Excessive Wear
Probable Causes | Actions or Countermeasures |
---|---|
Excessive interference - wide wear path. | Check seal ID and shaft size (interference). |
Excessive radial force - wide wear path | Check for high radial load. Look for small ID garter spring. |
Excessive pressure on lip - concave wear path. | Check system pressure at operation conditions. |
Rough shaft finish. | Inspect shafts for defects. Measure surface finish. |
Insufficient lubrication at seal lip. | Provide lubrication on air side of seal or between lips |
Eccentric Wear
Probable Causes | Actions or Countermeasures |
---|---|
Seal cocked in assembly. | Check shaft for wide wear path. Check installation procedure and equipment. |
Excessive radial wall variation of lip. | Measure seal radial wall variation and relate to wear pattern. |
Excessive shaft to bore misalignment. | Check shaft to bore offset. |
Angled or cocked shaft. | Check shaft alignment, excessive run-out or bent shaft. |
Side load applied to shaft. | Check possible side deflection or lose bearings. |
Below is an example of eccentric wear. As you can see, the wear path is wider on one side.
Nicks, Scratches or Cuts at Lip Contact Area
Probable Causes | Actions or Countermeasures |
---|---|
Sharp edge or burrs on end of shaft. | Inspect shaft for burrs or sharpness. |
Sharp edge or burrs on installation tool. | Check installation device for sharp edges or burrs. |
Seal installed over keyway or splines. | Provide installation sleeve for splines or keyways |
Trimming knife cuts. | Check suppliers knife trimming methods. |
Nibbled appearance at sealing edge. | Defects may be caused by bulk finishing or handling by supplier. |
Cuts from packing methods. | Check suppliers packaging and shipping methods. |
Below is an example of a cut seal lip.
Tears or Separations in Lip Area
Probable Causes | Actions or Countermeasures |
---|---|
Stress fatigue in flex section. | Check system pressure. Seal may be deformed in ID flex section. |
Bond separation at ID of metal case. | Check seal for bond, burrs, and blisters. |
Migration of low temperature crack. | Check lip contact area of minor cold cracks. Suspect severe side load at lot temperatures. |
Circumferential tear behind lip. | Look behind lip at base for circumferential tear caused by pressure or fatigue. |
Caused during assembly or removal. | Review teardown and seal removal methods and check tools used. |
Below is an example of poor bond. You will know if you have a bond problem when the separation between the rubber and metal component is "Clean" and there are no rubber particles attached to the metal component .
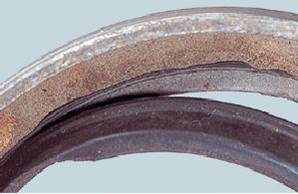
Hardening or Cracking of Rubber
Probable Causes | Actions or Countermeasures |
---|---|
Prolonged or excessive high temperature exposure. | Check rubber spec. versus system temperature profile. |
Flexing of lip at low temperatures below rubber capability. | Check rubber spec. versus system temperature profile. Check offset, runout, and sideplay. |
Extended dry running causing localized high temperature under the lip. | Check fluid level. Check for shaft that is too smooth. |
Cracking from disassembly or observation techniques. | Review procedures and look for other damage. |
Ozone exposure. | Check other dry areas of rubber. Consider excessive solar or electrical exposure. |
Below is an example of a seal that has signs of heat cracking.
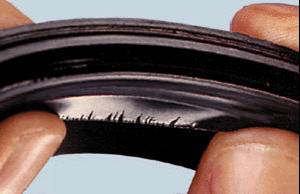
Measure ID and Radial Load
Probable Causes | Actions or Countermeasures |
---|---|
Measure ID using non contact device. | Use optical comparator or linear scope. Record min/max readings and relate to leak. |
Measure wear pattern width and variation. | Use optical means, photographic, or cross section in comparator. |
Compare profile with profile of unused seal. | Section seal and mount on glass slide for magnified comparator viewing. |
Measure radial ID force. | Use electronic split mandrel type radial load device. |
Cocked Oil on Lip
Probable Causes | Actions or Countermeasures |
---|---|
Hard and glazed deposit in ID. | Possibly decomposed fluid. Scrape off and analyze. |
Insufficient hydrodynamic pumping action. | Helices ineffective. |
Excessive under lip temperature. | Check specification of fluid versus operating parameters. |
Softening or Swelling
Probable Causes | Actions or Countermeasures |
---|---|
Volume change of material very high. | Refer to elastomer physical data and check fluid. |
Reversion. | Check elastomer/fluid compatibility specification. |
Exposure to solvent used during teardown. | Review teardown procedure and elastomer compatibility with solvents. |
Operational contamination of fluid being sealed. | Check for possible exposure to unspecified media coming in contact with seal. |
Below is an example of a seal with fluid compatibility problems.
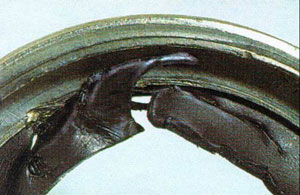
Inverted Lip Due to Poor Installation
Probable Causes | Actions or Countermeasures |
---|---|
Oil to air side shaft assembly. | Provide installation aid such as a bullet nose for shaft. |
Lack of proper concentricity assembly. | Provide centering aide for assembly such as locating pins. |
Login
News
February 23rd
Here is a great article on grease compatibility . . .
The Skinny on Grease Compatibility
July 30th
Here is a link to a great article about how to avoid particulate contamination . . . Obviously it goes without saying that a sealing...
How to Avoid Particulate Contamination